Our gloves manufacturing process is strictly controlled through in-house Quality Control (QC) and Quality Assurance (QA) in every steps from raw material sourcing up to the distribution. All our production lines are subjected to continuous improvement to ensure smooth running and garantee consistency in the quality of our gloves. On-line quality control standards have been implemented throughout the manufacturing process to ensure products of the highest quality.
RAW MATERIAL TEST
Testing and analysis of raw material is performed in our well equipped laboratory or outsourced to our selected business partners who are operating conform international standards. All incoming raw material is subjected to detailed and stringent quality testing and analysis before being submitted to the compounding precess.
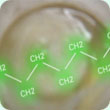 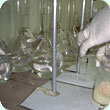 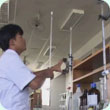 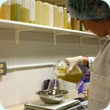
|
COMPOUNDING
The dispersion is prepared by ball mill technique with proper monitoring of time and other important aspects. Approved dispersion from our laboratory is mixed with latex according to our specification formulation. Compound latex is matured and tested to conform the specification before feeding to the production line.
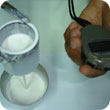 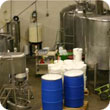 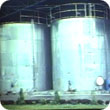 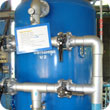
|
DIPPING
Moulds are cleaned with diluted HCL acid, NaOH and clean water, then they are dried and dipped first into the coagulant tank that contains process chemical. After becoming sufficiently dried, the moulds are being dipped into the compound latex. Both coagulant and compound latex tanks are properly checked for properties and conditions such as total solid content, temperature, level and etc.
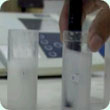 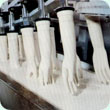 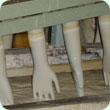 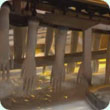 
|
LEACHING & VULCANIZING
Proper latex gel on moulds are beaded, further dried, and then leached into the Pre- Leach tank before properly vulcanized to ensure the best physical properties and reduce moisture content. All our gloves run through the Pre-Leaching and Post-Leaching processes into treated hot water at about 70 – 80°C with an overflow system. The Post-Leaching is to ensure the minimum latex protein level and to remove the extractable water soluble materials, chemical residue and non-rubber particles. Cyclone Tumbling is the final process of production. In this process, the gloves are tumbled for the final vulcanization process cycle with temperature and time critically controlled to low powder content and moisture level down to bear minimum.
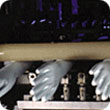 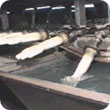 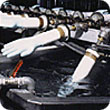 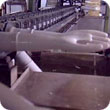 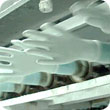
|
STRIPPING & TUMBLING
After the leached gloves are dipped into Wet Slurry tank of closely controlled for the bacteria build up and protein content, the gloves are finally stripped from the formers with our Auto-Stripping lines.
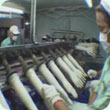 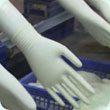 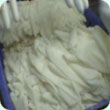
|
QUALITY CONTROL
On-Line quality control processes are performed by random sampling in every half hour for airtight inspection. Watertight test, pin-hole, physical properties, dimension measurement and aesthetics appeal are also arranged for process control. Our QC operators are well-trained in order to keep all aspects concerned in proper condition for releasing only good quality gloves to pack for our customers.
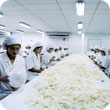 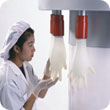 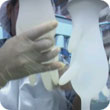 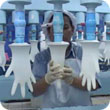 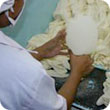
|
PACKING
Gloves Packing Section is dust free with hygienic filtered air system. Our packing operators further inspect to ensure no major visible defectives gloves are being packed. A hundred pieces of specific size will be first weighed and such weight will be made up for packing per box. The boxes are packed in well labeled cartons and delivered to customers subject to our pre-shipment QA inspection.
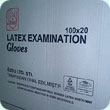 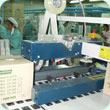 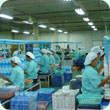 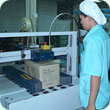
|
|